Dismiss Notice
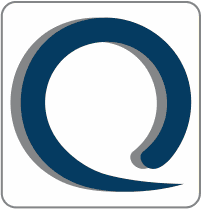
You must be a registered member in order to post messages and view/download attached files in this forum.
Click here to register.
Click here to register.
Training management on new ISO 9001:2015
Discussion in 'ISO 9001:2015 - Quality Management Systems' started by k_richer, Feb 10, 2017.
Page 1 of 2
Page 1 of 2