Dismiss Notice
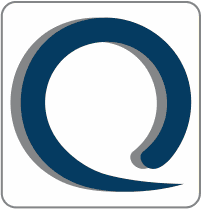
You must be a registered member in order to post messages and view/download attached files in this forum.
Click here to register.
Click here to register.
How many People work for your company
Discussion in 'ISO 9001:2015 - Quality Management Systems' started by Jamie Lill, Mar 17, 2016.
Page 2 of 2
Page 2 of 2