Dismiss Notice
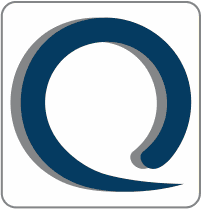
You must be a registered member in order to post messages and view/download attached files in this forum.
Click here to register.
Click here to register.
7.3.2 Employee motivation and empowerment
Discussion in 'IATF 16949:2016 - Automotive Quality Systems' started by Renata Osborne, Oct 16, 2019.
Page 1 of 2
Page 1 of 2