Dismiss Notice
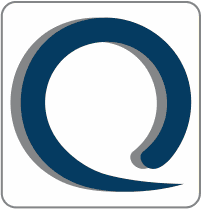
You must be a registered member in order to post messages and view/download attached files in this forum.
Click here to register.
Click here to register.
Why auditing using the "Process Approach" may not be enough...
Discussion in 'ISO 19011 - Auditing Management Systems Guidelines' started by Andy Nichols, Aug 28, 2015.