Dismiss Notice
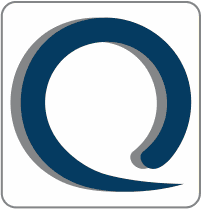
You must be a registered member in order to post messages and view/download attached files in this forum.
Click here to register.
Click here to register.
Weld callout question
Discussion in 'Manufacturing and Related Processes' started by S1D3K1CK, Feb 22, 2023.
Tags: