Dismiss Notice
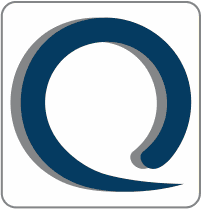
You must be a registered member in order to post messages and view/download attached files in this forum.
Click here to register.
Click here to register.
Thinking through a process validation
Discussion in 'Qualification & Validation (Also 21 CFR Part 11)' started by Candi1024, Mar 31, 2016.