Dismiss Notice
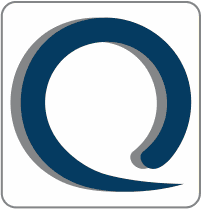
You must be a registered member in order to post messages and view/download attached files in this forum.
Click here to register.
Click here to register.
Removing Non Value Added Inspection
Discussion in 'ISO 13485 and ISO 14969 – Medical Devices QMS' started by pcmc47, Jan 29, 2016.
Tags: