Dismiss Notice
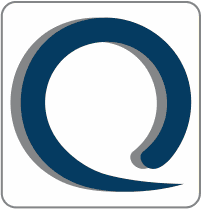
You must be a registered member in order to post messages and view/download attached files in this forum.
Click here to register.
Click here to register.
Relationship between PFMEA & Control Plan for Special Characteristics
Discussion in 'FMEA - Failure Modes and Effects Analysis' started by Pongsakorn, Jun 1, 2016.