Dismiss Notice
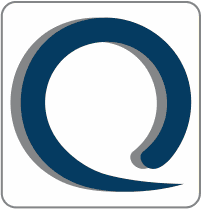
You must be a registered member in order to post messages and view/download attached files in this forum.
Click here to register.
Click here to register.
Quality Department Development
Discussion in 'Other Quality and Business Related Topics' started by Kristof, Sep 28, 2023.