Dismiss Notice
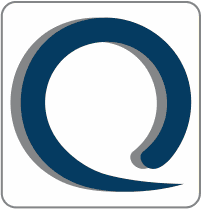
You must be a registered member in order to post messages and view/download attached files in this forum.
Click here to register.
Click here to register.
Negative leak rate during testing and R & R issues
Discussion in 'Gage R&R and MSA - Measurement Systems Analysis' started by Rajesh A, Oct 8, 2015.