Dismiss Notice
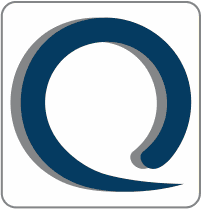
You must be a registered member in order to post messages and view/download attached files in this forum.
Click here to register.
Click here to register.
Mold qualification on different machines
Discussion in 'Qualification & Validation (Also 21 CFR Part 11)' started by jojo63, Jan 11, 2016.