Dismiss Notice
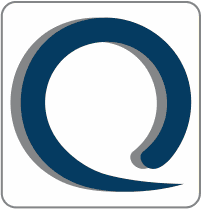
You must be a registered member in order to post messages and view/download attached files in this forum.
Click here to register.
Click here to register.
Metal Fabrication - Sampling Inspection
Discussion in 'Sampling, Standards and Inspection' started by Olivier Maudhuit, Feb 18, 2020.