Dismiss Notice
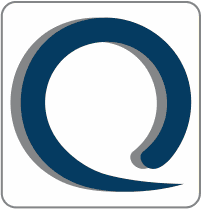
You must be a registered member in order to post messages and view/download attached files in this forum.
Click here to register.
Click here to register.
Management Review acc. to ISO9001:2015 - example
Discussion in 'ISO 9001:2015 - Quality Management Systems' started by Kristof, Aug 13, 2018.