Dismiss Notice
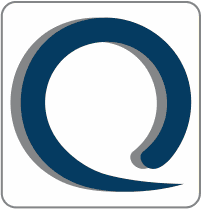
You must be a registered member in order to post messages and view/download attached files in this forum.
Click here to register.
Click here to register.
Let's talk Communication Boards
Discussion in 'Lean, Six Sigma and DFSS' started by Candi1024, Dec 18, 2015.