Dismiss Notice
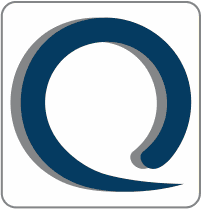
You must be a registered member in order to post messages and view/download attached files in this forum.
Click here to register.
Click here to register.
Layered Process Audits; How to prevent them from being the "Flavor of the Month"
Discussion in 'Process Audits and Layered Process Audits' started by Marcusja2002, Oct 9, 2015.