Dismiss Notice
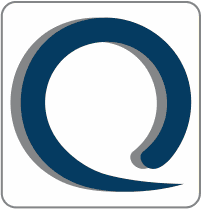
You must be a registered member in order to post messages and view/download attached files in this forum.
Click here to register.
Click here to register.
Internal Audit
Discussion in 'ISO 9001:2008 - Quality Management Systems' started by Kunle Ogunola, Dec 15, 2015.
Page 2 of 2
Page 2 of 2