Dismiss Notice
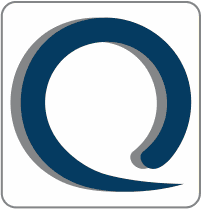
You must be a registered member in order to post messages and view/download attached files in this forum.
Click here to register.
Click here to register.
How long is a piece of…
Discussion in 'ISO 19011 - Auditing Management Systems Guidelines' started by Andy Nichols, Jul 2, 2023.
Tags: