Dismiss Notice
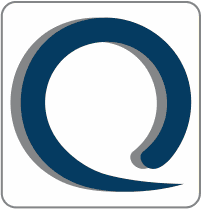
You must be a registered member in order to post messages and view/download attached files in this forum.
Click here to register.
Click here to register.
How do I ensure certain materials are not used?
Discussion in 'Manufacturing and Related Processes' started by Nikki, May 17, 2018.