Dismiss Notice
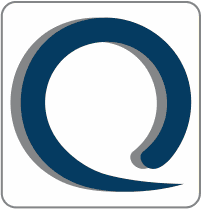
You must be a registered member in order to post messages and view/download attached files in this forum.
Click here to register.
Click here to register.
Help with explaining the QMS to other peers
Discussion in 'ISO 9001:2015 - Quality Management Systems' started by Steph, Jul 18, 2016.