Dismiss Notice
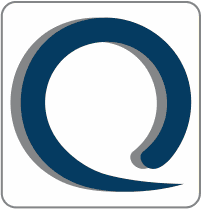
You must be a registered member in order to post messages and view/download attached files in this forum.
Click here to register.
Click here to register.
Hello all. New QSM requiring help!!
Discussion in 'New Member Introductions' started by FreshFish1975, Mar 30, 2016.