Dismiss Notice
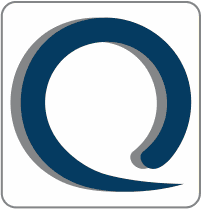
You must be a registered member in order to post messages and view/download attached files in this forum.
Click here to register.
Click here to register.
haven't considered which chart should i use
Discussion in 'SPC - Statistical Process Control' started by klauss1, Feb 1, 2024.