Dismiss Notice
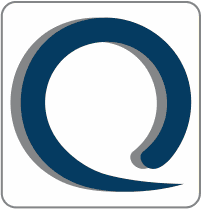
You must be a registered member in order to post messages and view/download attached files in this forum.
Click here to register.
Click here to register.
evaluation of the process produced on the another machine
Discussion in 'Capability - Process, Machine, Gage …' started by essegn, Jul 30, 2019.