Dismiss Notice
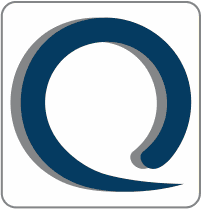
You must be a registered member in order to post messages and view/download attached files in this forum.
Click here to register.
Click here to register.
Define standard order and non-standard order
Discussion in 'Other Quality and Business Related Topics' started by MKKIM, Feb 7, 2023.