Dismiss Notice
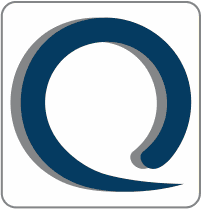
You must be a registered member in order to post messages and view/download attached files in this forum.
Click here to register.
Click here to register.
Cpk to percent and to Yield calculation
Discussion in 'Lean, Six Sigma and DFSS' started by essegn, Sep 3, 2018.