Dismiss Notice
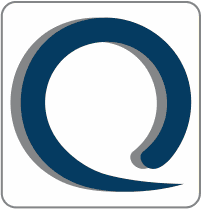
You must be a registered member in order to post messages and view/download attached files in this forum.
Click here to register.
Click here to register.
AS9100 7.1.5.2 Measurement Tracability
Discussion in 'AS 91XX - Aerospace Quality Standards' started by Laura N., Feb 28, 2020.