Dismiss Notice
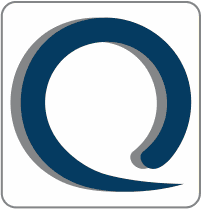
You must be a registered member in order to post messages and view/download attached files in this forum.
Click here to register.
Click here to register.
Approaches to creation of control plan
Discussion in 'APQP and PPAP' started by Plague Doctor, May 30, 2016.
Tags: