Dismiss Notice
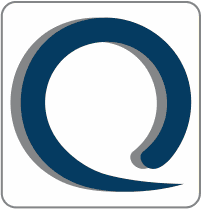
You must be a registered member in order to post messages and view/download attached files in this forum.
Click here to register.
Click here to register.
ANSI/ASQ Z1.9 Sampling Standard
Discussion in 'Sampling, Standards and Inspection' started by Mike S, Jan 11, 2016.
Tags: