Dismiss Notice
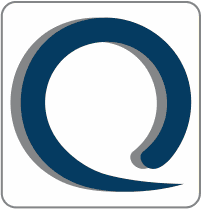
You must be a registered member in order to post messages and view/download attached files in this forum.
Click here to register.
Click here to register.
Acceptance sampling for Raw Material Receving
Discussion in 'ISO 9001:2015 - Quality Management Systems' started by Manish Sawant, Mar 28, 2016.