Dismiss Notice
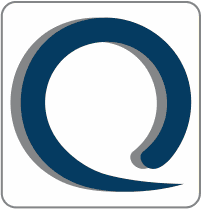
You must be a registered member in order to post messages and view/download attached files in this forum.
Click here to register.
Click here to register.
9.2.2.1 Internal audit program
Discussion in 'IATF 16949:2016 - Automotive Quality Systems' started by bkirch, Oct 3, 2017.