Dismiss Notice
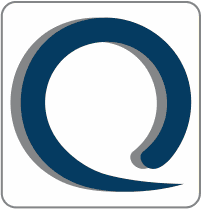
You must be a registered member in order to post messages and view/download attached files in this forum.
Click here to register.
Click here to register.
6.4.8 Calibration Labels
Discussion in 'ISO 17025 - Calibration and Test Laboratories' started by Carlee Gruizinga, Oct 25, 2023.