Dismiss Notice
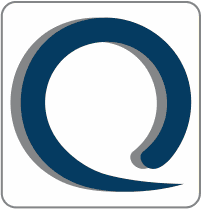
You must be a registered member in order to post messages and view/download attached files in this forum.
Click here to register.
Click here to register.
4140 hardness change mystery
Discussion in 'Manufacturing and Related Processes' started by EagleQuality, Apr 27, 2016.