Dismiss Notice
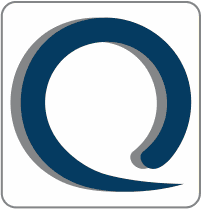
You must be a registered member in order to post messages and view/download attached files in this forum.
Click here to register.
Click here to register.
What should be Maximum Cpk value?
Discussion in 'Capability - Process, Machine, Gage …' started by Pongsakorn, Dec 27, 2016.