Dismiss Notice
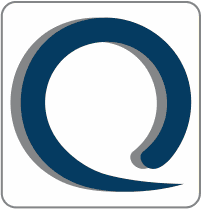
You must be a registered member in order to post messages and view/download attached files in this forum.
Click here to register.
Click here to register.
Visual Inspection
Discussion in 'Sampling, Standards and Inspection' started by essegn, Apr 23, 2018.