Dismiss Notice
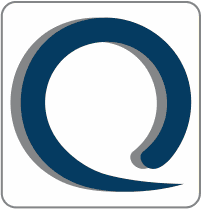
You must be a registered member in order to post messages and view/download attached files in this forum.
Click here to register.
Click here to register.
Simple Explanation for AQL VS LTPD
Discussion in 'Sampling, Standards and Inspection' started by Pongsakorn, Jul 7, 2016.