Dismiss Notice
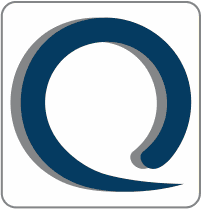
You must be a registered member in order to post messages and view/download attached files in this forum.
Click here to register.
Click here to register.
Root cause is never the person .... REALLY???
Discussion in '5S, 5Why, 8D, TRIZ, SIPOC, RCA, Shainin Methods...' started by ncwalker, Jan 14, 2016.
Page 1 of 4
Page 1 of 4