Dismiss Notice
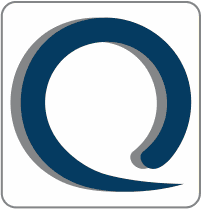
You must be a registered member in order to post messages and view/download attached files in this forum.
Click here to register.
Click here to register.
Quality Management software with cost tracking
Discussion in 'Coffee Break and Community Discussion Forum' started by Elliot A. Goode, Aug 28, 2017.