Dismiss Notice
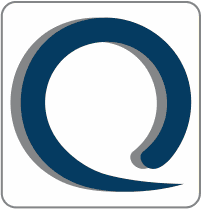
You must be a registered member in order to post messages and view/download attached files in this forum.
Click here to register.
Click here to register.
Procedure for Change Management
Discussion in 'IATF 16949:2016 - Automotive Quality Systems' started by sergiu, Aug 1, 2019.
Tags: