Dismiss Notice
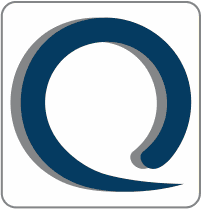
You must be a registered member in order to post messages and view/download attached files in this forum.
Click here to register.
Click here to register.
PFMEA in low volume medical device manufacturing
Discussion in 'ISO 13485 and ISO 14969 – Medical Devices QMS' started by Renaz, Oct 20, 2018.