Dismiss Notice
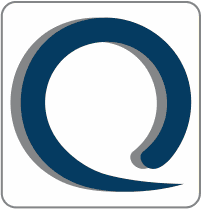
You must be a registered member in order to post messages and view/download attached files in this forum.
Click here to register.
Click here to register.
Need Proof that operators that use gage and make parts need to do MSA
Discussion in 'Gage R&R and MSA - Measurement Systems Analysis' started by Mark Paul, Aug 10, 2016.