Dismiss Notice
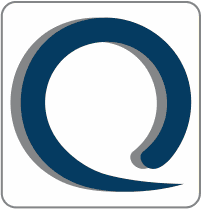
You must be a registered member in order to post messages and view/download attached files in this forum.
Click here to register.
Click here to register.
Moving a Steel Production Plant
Discussion in 'Other Quality and Business Related Topics' started by claudiogut, Dec 2, 2023.
Tags: