Dismiss Notice
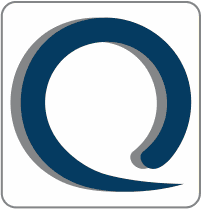
You must be a registered member in order to post messages and view/download attached files in this forum.
Click here to register.
Click here to register.
ISO 13485 7.4.1 Purchasing Process
Discussion in 'ISO 13485 and ISO 14969 – Medical Devices QMS' started by Jura1752, Aug 7, 2016.