Dismiss Notice
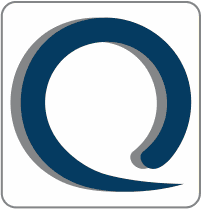
You must be a registered member in order to post messages and view/download attached files in this forum.
Click here to register.
Click here to register.

CorrectSPC Gage Resolution Required for SPC
Inadequate gage resolution will destroy your SPC efforts!