Dismiss Notice
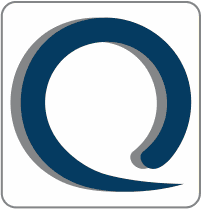
You must be a registered member in order to post messages and view/download attached files in this forum.
Click here to register.
Click here to register.
Early Launch Containment plan
Discussion in 'APQP and PPAP' started by QMSmaster, Jan 20, 2016.