Dismiss Notice
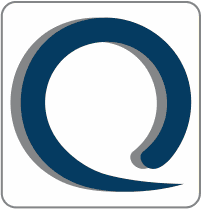
You must be a registered member in order to post messages and view/download attached files in this forum.
Click here to register.
Click here to register.
Doing Less Change Orders by Allowing Part Interchangeability
Discussion in 'ISO 13485 and ISO 14969 – Medical Devices QMS' started by John Thacher, Dec 16, 2020.