Dismiss Notice
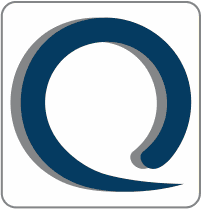
You must be a registered member in order to post messages and view/download attached files in this forum.
Click here to register.
Click here to register.
Do we have to validate every piece of new equipment?
Discussion in 'ISO 13485 and ISO 14969 – Medical Devices QMS' started by Nikki, Apr 18, 2016.