Dismiss Notice
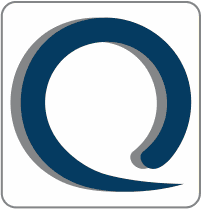
You must be a registered member in order to post messages and view/download attached files in this forum.
Click here to register.
Click here to register.
Correction actions implemented vs 'intent'.
Discussion in 'ISO 9001:2015 - Quality Management Systems' started by MonsterEnergy22, Jan 17, 2024.