Dismiss Notice
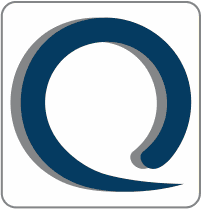
You must be a registered member in order to post messages and view/download attached files in this forum.
Click here to register.
Click here to register.
Clause 4.4: ISO9001:2015 Performance Indicators
Discussion in 'ISO 9001:2015 - Quality Management Systems' started by Lonewalker, Dec 20, 2016.