Dismiss Notice
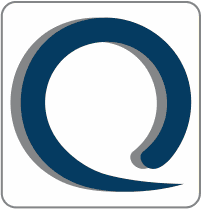
You must be a registered member in order to post messages and view/download attached files in this forum.
Click here to register.
Click here to register.
Clarification of Section 8.4-Control of Externally Provided Processes
Discussion in 'ISO 9001:2015 - Quality Management Systems' started by mojojojo78, Aug 15, 2022.