Dismiss Notice
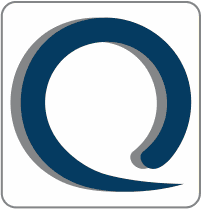
You must be a registered member in order to post messages and view/download attached files in this forum.
Click here to register.
Click here to register.
Approving Suppliers
Discussion in 'AS 91XX - Aerospace Quality Standards' started by Robert Sisneros, Oct 10, 2023.