Dismiss Notice
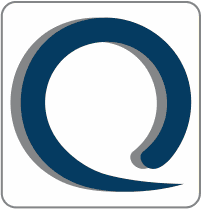
You must be a registered member in order to post messages and view/download attached files in this forum.
Click here to register.
Click here to register.
8.4.2.5 Supplier development
Discussion in 'IATF 16949:2016 - Automotive Quality Systems' started by Chandrasekhar T, Jun 13, 2018.